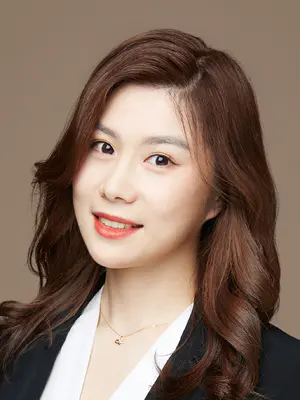
Ms. Vivian Feng
PM
Phone | +86 10 5867 7200 |
---|---|
Fax | +86 10 5867 7126 |
vivian.feng@hjtexpo.com | |
Address | Room 2003, Building A, Timecourt, Chaoyang District, Beijing |
Orthopaedic implants play a critical role in improving the lives of patients with bone and joint issues. As demand for these implants continues to rise, so does the need for proper cleaning and packaging procedures to ensure the safety and efficacy of these devices.
Cleaning of orthopaedic implants is an essential step to achieve their biocompatibility and control the microbiological load required for their sterilization process. It is crucial to use effective cleaning methods that do not impair the biocompatibility or performance of the implant. On the other hand, packaging is used to preserve orthopaedic implants from contamination and damage during shipping, handling, and storage. Additionally, final packaging has the purpose of maintaining the sterility of the implant, serves as a means of identification and labelling, and ensures traceability from production to implantation.
A webinar on “Cleaning and packaging of coated orthopaedic implants” was organised on April 12, 2023 by Lincotek Medical Wuxi, in partnership with Ringier Events, and emphasized the importance of proper final cleaning and packaging processes to ensure compliance with stringent implant quality regulations. The speaker, Dr. Zakaria El Koura, Consultant at Lincotek Medical Wuxi, shares with International Plastics News for Asia, some highlights of his presentation.
Please provide an overview on plasma spray coating and its function.
Dr. El Koura: While plasma spray coating is not the central part of my presentation, understanding the process and its main features is essential for defining subsequent cleaning and packaging procedures and establishing a common foundation for discussion. Thermal spray coating is a very mature technology with over 40 years of history and wide usage. Orthopedic implants come in various shapes, morphologies, and serve different purposes.
The central element of the plasma spray equipment is the torch, which plays a vital role in the process. It generates a plasma plume that is used for melting the titanium or hydroxyapatite powder introduced through a feeder. These molten particles are subsequently propelled onto a substrate (the implant), where they undergo a cooling and solidification process, resulting in the formation of the plasma spray coating. It is crucial to highlight the exceptionally high temperatures achieved within the plasma, which are essential for ensuring the sterility of the coated implants. The torch body is cooled by a continuous flow of water to maintain its operational stability.
Plasma spray coatings can be classified based on the environmental conditions surrounding the torch. When operating in the presence of air, it is commonly referred to as air plasma spray. Conversely, if a vacuum is created around the torch during the coating process, it is known as vacuum plasma spray. These two types of coatings exhibit distinctive properties and features. However, it is worth noting that both types of coating have been extensively utilized for long time and have consistently demonstrated their safety and effectiveness in the field of medical devices.
What are the types of materials used for this process?
Dr. El Koura: Coatings can be classified based on the materials used, such as titanium coating, hydroxyapatite (HA) coating, or a combination of both (double coating). Each type of coating possesses distinct properties that need to be considered when determining the appropriate final cleaning and packaging procedures. Titanium coating results in rough and porous surfaces, posing challenges in terms of contamination removal and preservation of packaging integrity. Cleaning such surfaces can be particularly difficult due to the need to eliminate contaminants from uneven surfaces. Additionally, the roughness of titanium coatings can potentially cause damage to the packaging materials.
On the other hand, hydroxyapatite coating is biocompatible, promotes osteointegration, and exhibits lower porosity and roughness compared to titanium coatings. However, hydroxyapatite coatings are brittle and fragile, rendering them unsuitable for cleaning using ultrasound techniques as they could harm the coating. Many of our customers rely on Lincotek Medical to perform the final cleaning of hydroxyapatite-coated implants since they lack the expertise and equipment required for this task. That's why I emphasized in my presentation that Lincotek Medical has developed a specialized cleaning process.
In essence, the objective of the final cleaning process is to eliminate any residue, minimize bacterial and endotoxin contamination, while ensuring that the cleaning procedure does not alter the medical device or the delicate coating, especially in the case of HA. Lincotek Medical has implemented an advanced cleaning process that adheres to the necessary standards.
How does Lincotek Medical perform the cleaning and packaging processes? How do these processes comply with international standards?
Dr. El Koura: In my virtual presentation, my main focus is on achieving compliance and ensuring the quality of cleaning and packaging processes. Compliance with quality standards is of utmost importance in the medical device industry, and there are specific standards that we adhere to. One key standard is ISO 13485, which outlines the requirements for the quality management system of medical device companies. It encompasses all the steps involved in the production of medical devices within the company. Another commonly used standard is ISO 19227, which ensures the cleanliness of orthopedic implants and was published in 2018.
To meet these standards, we begin with a risk evaluation and a cleanliness evaluation of the parts and components according to ISO 19227. All processes undergo validation, including defining the worst-case scenarios, determining sample sizes, and continuous monitoring. Additionally, for cleaning validation, we utilize other standards that pertain to specific tests performed as part of our validation process. We have discussed case studies from our internal validations during the presentation.
At Lincotek, our approach involves thoroughly validating each step of the medical device production process and identifying potential contaminants. We ensure that our validation and equipment are capable of effectively removing these contaminants. We request our customers to send us parts that are free from any residues. If we find hollows or contaminations inside the parts during inspection, we return them to the customers as we cannot work on such parts. This comprehensive evaluation and cleanliness assessment are conducted for each step at Lincotek Medical. We also have trained personnel who perform inspections to ensure that there are no residues from the manufacturer's processes. If any residues from other processes are present, we return the part to the manufacturer.
During the coating process, the part is exposed to very high temperatures, resulting in zero contamination as the high temperatures effectively sterilize and eliminate any contaminants. Following the coating process, our team at Lincotek Medical performs unmasking and cleans the part with alcohol to remove any masking residues from the surfaces. The parts are then blown with compressed air. Once the finishing process is complete, the parts are ready for final packaging.
As for packaging, we adhere to several standards, including ISO 11607 (Part 1 and Part 2), which outline the general requirements for packaging validation. Additionally, we comply with Chinese Standards YY/TO698 and O681, which also pertain to packaging validation. Lincotek Medical offers a comprehensive service that includes both coating and packaging of medical devices. We have validated and continuously monitor our cleaning equipment and processes, clean rooms, and packaging equipment. Our cleaning and packaging processes fully meet the most up-to-date standards and regulatory requirements. We can supply both temporary and final packaging solutions. Finally, it's worth mentioning that Lincotek Medical has over 20 years of experience in cleaning and packaging coated orthopedic implants, allowing us to assist our clients in overcoming the numerous challenges throughout the entire process.
PM
Phone | +86 10 5867 7200 |
---|---|
Fax | +86 10 5867 7126 |
vivian.feng@hjtexpo.com | |
Address | Room 2003, Building A, Timecourt, Chaoyang District, Beijing |
PM
Phone | +86 10 5867 8210 |
---|---|
Fax | +86 10 5867 7126 |
doria.fang@hjtexpo.com | |
Address | Room 2003, Building A, Timecourt, Chaoyang District, Beijing |
Please browse vertically for better experience.